GYROFLEX
GYROFLEX Ultimate Multitasking Machine
The GYROFLEX Automated Multitasking Machine increases parts processing efficiency, accuracy and flexibility. Featuring Fuji legendary automation, the Gyroflex offers the size, rigidity and productivity necessary to handle simple to complex workpieces.
- Built-in FUJI LX-40 high-speed 3-axis gantry robot
- Dual opposed main spindles
- Exceptionally rigid, productive and flexible
- Machines complex parts efficiently and accurately
- Performs parts prototyping, plus high-volume and high-mixed production
- Reduced setup, changeover, and part transfer times
- B-axis high performance milling tool spindle with 15 HP and 12,000 MAX RPM
- Two 15-station live tool turrets mounted on the highly rigid X & Y axis box way slides
Process Combination
The standard capacity of 30 tools on the turrets (15 each) and 40 tools on the ATC magazine enables increased machining functionality and flexibility for high mixed production by process combination.
Floor space reduction can be realized by machining with one single machine.
Integrated Robot for Unattended Operation Integrated robot provides fast parts handling and unattended operation. The hydraulic robot chuck enables stable clamping for heavy parts and eliminates any potential operator loading error.
Perfect chip disposal design enables non-stop and efficient production.
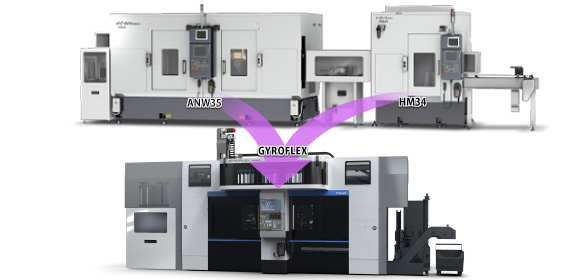
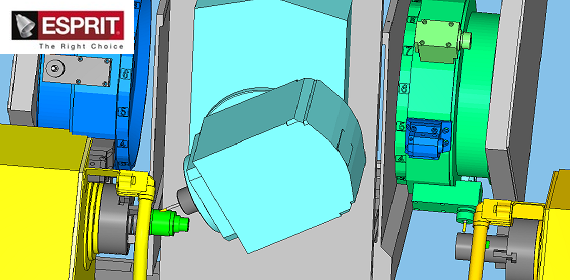
Programming Support
Easy programming for complex parts and process combination are possible with ESPRIT 3D CAD/CAM system.
Machine Structure
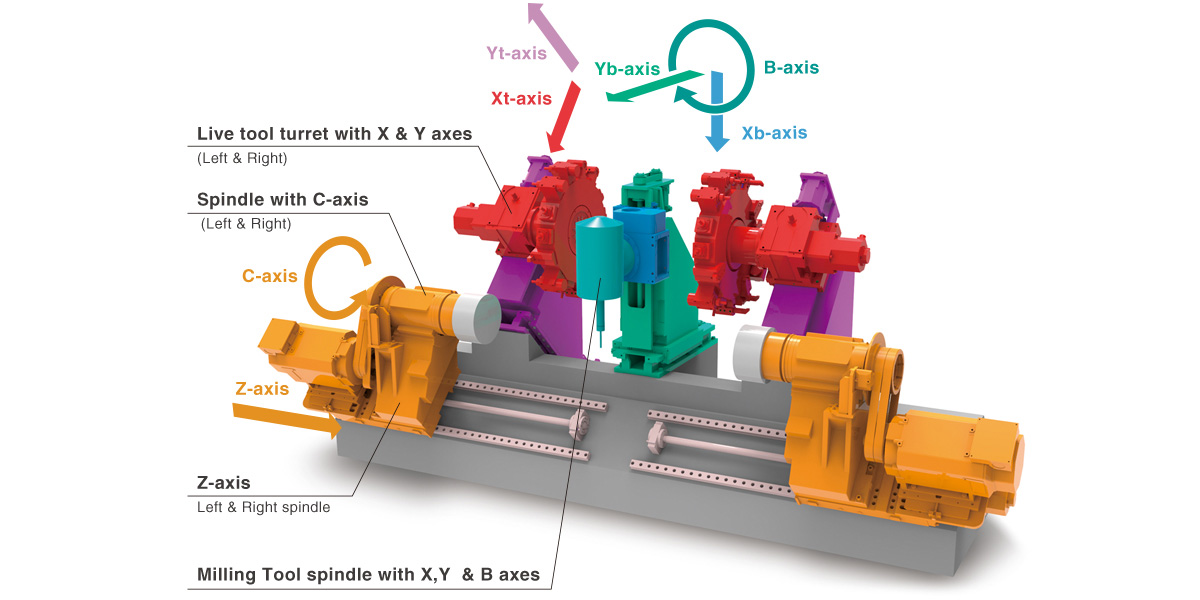
Live Tool Turret
- 15-station live tool turrets
- Mounted on highly rigid X & Y axis box way slides
- Turret index time: 0.4 sec
- Rigid turret clamping with hydraulic curvic coupling design
- Live tools designed for heavy cutting
- Spindle speed: Max 4,000 rpm
- Spindle motor: 6 HP
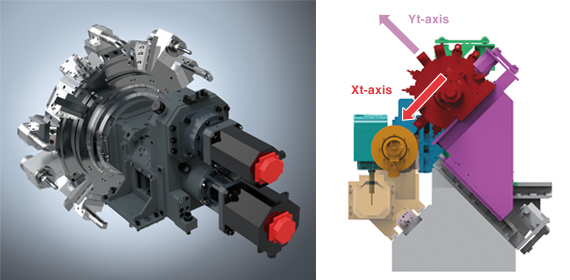
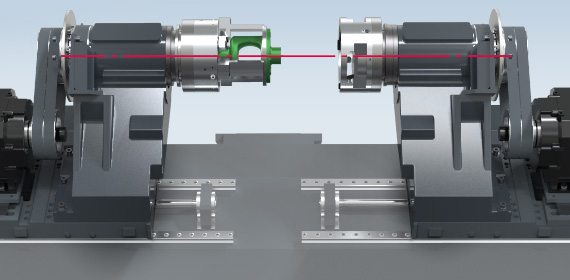
Main Spindle with C-Axis
- Opposed twin spindles positioned on Z-axis slide ways with 960mm of stroke
- Both spindles are equal in size and machining capability
- Same operations (OP-10A/10B) are possible on both spindles
- The 1st spindle can pass a part to the 2nd spindle while maintaining positioning accuracy
- The Z-axis slide can move at high speeds to reduce loading time to the 2nd spindle
Milling Tool Spindle
- Mounted on rigid X & Y axis box way slides
- Accesses both Z-axis spindles and swings up to 190 degrees, allowing for various types of machining
- Capto C6 standard equipment
- Tool and B-axis clamped by curvic coupling
- High performance milling tool spindle
- Spindle speed: 12,000 rpm
- Spindle motor: 15 HP
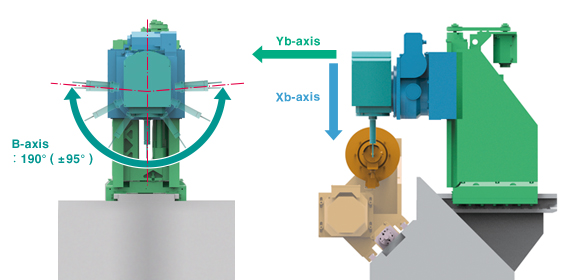
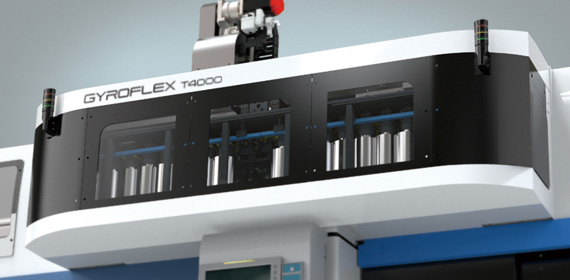
ATC
- ATC magazine located at the top of the machine for easy access and operation
- 40-tool magazine
- Rapid tool change time: 4 sec
- Maximum tool diameter: 130 mm
- Tool length: 300 mm
- Tool weight: 8 kg
3-Axis Gantry Robot
- Accesses peripheral devices at the left and right sides of the machine
- Two arms (primary and secondary) reduce machine overall height
- Hydraulic robot chuck enables stable clamping and workpiece handling with minimum space requirements due to the innovative thin type double hand design
- Robot chuck clamp confirmation sensor available as an option
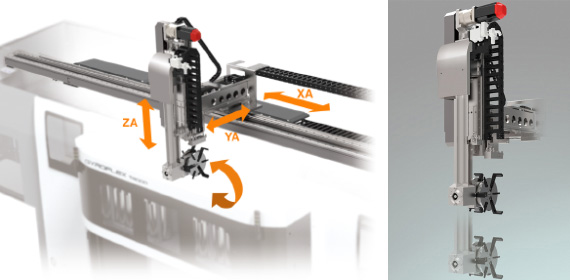